Don't miss our holiday offer - 30% OFF!
5 Key Elements of Efficient Stone Crusher Plant Layout Design
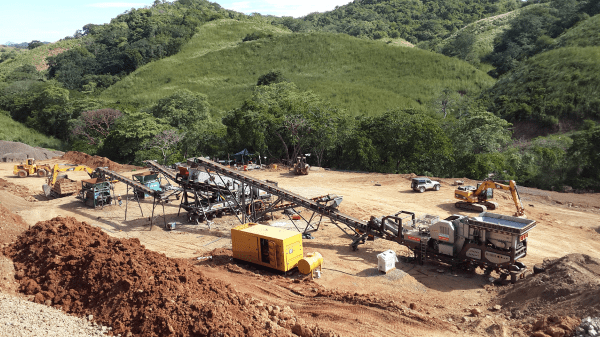
Introduction
The design of a stone crusher plant is instrumental in determining the operational efficiency and profitability of the operation. An optimized layout not only maximizes production rates but also reduces operating costs and promotes a safer working environment. It also allows for future expansion and ensures the plant can adapt to varying demand without significant downtime. The layout encompasses not just the physical placement of equipment but also the interconnectivity of different phases of the crushing process, ensuring a seamless transition from one stage to the next.
The stone crushing process typically involves several stages, each responsible for reducing rock to the desired size and separating unwanted material. The primary stage focuses on reducing large rocks into smaller sizes. Secondary and tertiary stages further reduce rock sizes and refine the material, often resulting in different grades of aggregate suitable for various uses. The efficiency of these stages directly affects the quality of the final product and the overall productivity of the plant. Variability in the raw material and stringent environmental regulations add layers of complexity to the design of a stone crusher plant.
Zenith is a well-established name in the mining equipment industry, renowned for its innovative technology, robust machinery, and exceptional customer service. With a history spanning decades, Zenith has developed a deep understanding of the mining sector’s challenges and opportunities, which is reflected in its product offerings. Zenith’s comprehensive range of crushing and screening equipment is designed to meet the toughest demands of the industry while providing high efficiency and low operational costs. Recognized for its global reach, Zenith offers unmatched support and service to clients worldwide, ensuring that customers have access to the best in class equipment and expert assistance whenever needed. As we delve into the key elements of stone crusher plant layout, Zenith’s products and solutions will be highlighted for their relevance in building an efficient, optimized plant.
With the introduction in place, the article will proceed to explore the five key elements of an efficient stone crusher plant layout, emphasizing how Zenith’s product offerings integrate into each aspect to enhance the overall functionality and productivity of the operation.
Element 1: Optimal Equipment Configuration
Significance of Selecting the Right Stone Crushers
The core of any stone crusher plant layout is the selection of the right types of crushing equipment. The choice of crushers and their configuration plays a critical role in determining the efficiency, final product quality, and scalability of the plant. Different types of crushers, such as jaw crushers, cone crushers, impact crushers, and others, are designed for specific primary, secondary, or tertiary crushing tasks. The compatibility of the crusher types with the material characteristics and the desired output cannot be overstated.
Zenith’s Product Range and Integration into Layout
Zenith’s extensive range of crushers is engineered to meet a variety of applications, ensuring that each stage of the crushing process is optimized for the highest efficiency and performance. Zenith offers:
- Jaw Crushers for robust primary crushing of hard materials with excellent reduction ratios
- Cone Crushers that provide secondary and tertiary crushing with precise shape and high-quality aggregate production
- Impact Crushers for achieving high reduction ratios and producing cubically-shaped materials suitable for construction and road building
Each crusher type from Zenith is designed for ease of maintenance, high durability, and seamless integration into a cohesive plant layout.
Considerations for Stationary vs. Mobile Crushing Plants
When designing an efficient stone crusher plant layout, it is crucial to consider whether a stationary or mobile crushing plant is more appropriate. Zenith offers both options:
- Stationary Crushing Plants are ideal for long-term projects or locations where the stone material is sourced from the same quarry over an extended period. These installations typically offer higher capacity and more customization options for the layout.
- Mobile Crushing Plants provide flexibility and are best suited for projects with shorter durations or where the plant needs to be relocated frequently. Zenith’s mobile crushers are designed for quick setup and can be easily adapted to changing project needs.
The choice between stationary and mobile should take into account factors such as the project duration, material source proximity, and the potential need for future relocation of the plant. Zenith can assist in making this decision by providing expertise and a wide range of solutions to fit the specific requirements of the operation.
In summary, the optimal equipment configuration is paramount to achieving an efficient stone crusher plant layout, and Zenith’s products offer the versatility and performance needed to address the unique needs of any crushing operation.
Element 2: Effective Use of Space
Importance of a Compact Layout
Maximizing the use of space is crucial in any stone crusher plant layout. A compact design minimizes the footprint of the plant and reduces the distance material must be transported between different crushing stages. This not only cuts down on operational costs such as fuel and labor but also reduces the time taken to move material, which can significantly increase overall efficiency. Additionally, a well-thought-out spatial arrangement allows for easier access to machinery for maintenance and reduces the potential for material build-up or bottlenecks.
Zenith’s Solutions for Space-Saving Designs
Zenith’s advanced design solutions focus on creating compact, space-efficient plants that do not compromise on processing capability. Zenith offers modular plant options where crushers, screens, and conveyors are designed to fit together seamlessly, allowing for quick assembly and disassembly. The modular approach also enables plants to be easily expanded or reconfigured, ensuring that they can evolve in line with the changing needs of the quarry or project.
- Modular Crushing and Screening Plants: Zenith’s modular systems are tailored to create a dense layout that optimizes the use of available space, with equipment arranged for optimal material flow and accessibility.
- Portable Crushing Plants: For operations that require frequent site changes, Zenith’s portable plants provide the flexibility of mobile units with the robustness and performance of stationary systems.
Strategies for Organizing Crushers, Screens, and Conveyors
Effective organization of the core components of the stone crusher plant is vital for maintaining efficiency:
- The placement of crushers should be considered carefully to ensure that material is easily and efficiently fed into the crushing chamber without unnecessary handling.
- Screens should be located where they can sort crushed material without causing delays or cross-contamination between different sized aggregates.
- Conveyors must be strategically arranged to transport material with minimal lift and turns, which reduces power consumption and wear on the conveyor components.
Zenith’s experienced team can provide layout designs that optimize the placement of these components, ensuring that each part of the plant contributes to a harmonious and efficient operation.
In essence, effective use of space is about more than just the physical dimensions of the plant. It is about creating a design that considers the movement of material, the functionality of the equipment, and the accessibility for maintenance—all of which Zenith’s products and services are well-equipped to address.
Element 3: Material Flow Optimization
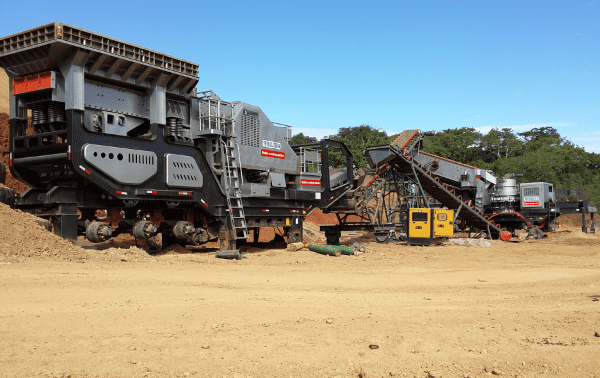
Ensuring Smooth Material Flow Through Each Crushing and Screening Stage
- Designing for direct feed to crushers to minimize transfer points
- Strategic placement of screening units for efficient sorting and material distribution
- Utilizing gravity flow where possible to move material efficiently
- Avoiding common bottlenecks by ensuring choke feeding in cone crushers and proper sizing in jaw crushers
Zenith’s Advanced Technologies for Managing Material Flow
- Integration of Zenith’s proprietary software for real-time monitoring and automatic adjustment of crushers and screens
- Utilization of Zenith’s advanced feeder systems that can adapt to varying material conditions
- Implementation of Zenith’s conveyor technology that optimizes belt speed to match processing rates, reducing spillage and blockages
- Adoption of Zenith’s latest innovations in dust suppression and noise reduction to enhance material handling
The Role of Feeders, Hoppers, and Discharge Systems in Maintaining Consistent Throughput
- Designing hoppers with sufficient storage capacity and compatible geometries to serve as a buffer and regulate the feed rate
- Using feeders capable of handling the expected load and compatible with the material characteristics to ensure a steady flow into the crushing equipment
- Implementing automated level control in hoppers and bins to prevent overflow and maintain a consistent material level
- Optimizing discharge systems, including chutes and transfer points, to facilitate a smooth transition and reduce wear on equipment
Each element of the material flow optimization process is critical for ensuring the plant operates at maximum productivity with minimal downtime. Zenith’s expertise and advanced technologies provide the necessary support to achieve these objectives, ensuring that the stone crusher plant layout is both functional and efficient.
Element 4: Integration of Automation and Control Systems
Benefits of Automated Process Control
Incorporating automation and control systems into a stone crusher plant layout brings numerous advantages, including enhanced productivity, consistent product quality, and reduced labor costs. Automation systems can monitor and adjust processing parameters in real-time, ensuring optimal performance across all stages of the crushing and screening process. This level of control can lead to more efficient use of energy, reduced wear on equipment, and the ability to quickly respond to changes in material characteristics or production requirements.
Zenith’s State-of-the-Art Control Systems
Zenith is at the forefront of integrating automation into its equipment, offering state-of-the-art control systems that provide several key benefits:
- Real-time Monitoring: Operators can oversee all aspects of the crushing process from a central control station, which can lead to quicker adjustments and more informed decision-making.
- Automated Adjustments: Zenith’s control systems can automatically adjust settings on crushers and screens based on real-time data, ensuring maximum efficiency and product consistency.
- Data Analytics: Advanced analytics provided by Zenith’s systems can help predict maintenance needs and optimize production schedules, reducing downtime and increasing plant longevity.
Examples of Real-Time Monitoring and Remote Control Capabilities
Zenith’s control systems are designed with user-friendly interfaces that allow for remote monitoring and control, which means operators can manage the plant even when they are not on-site:
- Remote Diagnostics: Zenith’s technology can diagnose issues remotely, allowing for quick intervention and reducing the need for on-site troubleshooting.
- Mobile Control Applications: Operators can use mobile devices to access plant controls, receive alerts, and view performance data, providing flexibility and convenience.
- Integration with Plant-Wide Management Systems: Zenith’s control systems can be integrated with larger plant management software, allowing for comprehensive oversight of the entire operation.
Incorporating Zenith’s advanced automation and control systems into a stone crusher plant’s layout not only streamlines operations but also enhances safety by reducing the need for manual intervention in potentially hazardous areas. This element of design is about harnessing technology to create a smart, efficient, and future-proof operation that can adapt to changing circumstances and maintain its competitiveness over time.
Element 5: Environmental Considerations and Safety
Implementing Environmental Safeguards
- Dust Suppression Techniques: Employ strategies like water mist systems, dust extraction units, and sealed transfer points to minimize airborne particles.
- Noise Reduction Measures: Incorporate sound barriers, vibration dampening materials, and noise enclosures around high-impact equipment to mitigate noise pollution.
- Sustainable Practices: Utilize energy-efficient motors and LED lighting, and consider renewable energy sources to reduce the plant’s environmental footprint.
- Recycling and Waste Management: Implement systems for recycling water used in dust suppression and segregate waste materials for responsible disposal or reuse.
Zenith’s Commitment to Eco-Friendly Equipment and Safety Features
- Eco-Friendly Technologies: Highlight Zenith’s innovations designed to reduce environmental impact, such as low-emission engines and biodegradable lubricants.
- Safety Integrations: Discuss Zenith’s safety features, including emergency stop buttons, guardrails, and pull cords on conveyors, as well as machine guards and lockout/tagout systems.
- Training and Support: Detail the training programs and support services provided by Zenith to ensure operators are well-versed in both environmental practices and safety protocols.
- Compliance with Regulations: Zenith’s equipment is engineered to meet international environmental and safety standards, ensuring compliance and reducing the risk of costly fines or shutdowns.
Planning for Safe Maintenance Access and Emergency Stop Mechanisms
- Maintenance Access: Design the plant layout with wide walkways, adequate lighting, and easy access to key maintenance points to ensure safety during routine and emergency servicing.
- Emergency Stop Mechanisms: Install clearly marked and accessible emergency stop buttons throughout the plant to allow for immediate shutdown in case of an incident.
- Regular Safety Audits: Schedule routine inspections and audits to identify potential hazards and ensure that all safety equipment is functioning correctly.
- Employee Involvement: Encourage a culture of safety by involving employees in identifying risks and developing mitigation strategies, fostering a sense of ownership over their work environment.
Environmental considerations and safety are not just regulatory obligations but are also integral to the sustainable operation of a stone crusher plant. Zenith’s products and services are designed with these priorities in mind, offering solutions that help plant owners maintain the highest standards of environmental care and safety.
Conclusion
To conclude, a well-designed stone crusher plant layout is fundamental for operational efficiency, encompassing optimal equipment selection, space utilization, material flow, automation integration, and adherence to environmental and safety protocols. Zenith’s product offerings, including a variety of crushers, screens, and advanced control systems, are essential in constructing a plant that is both productive and compliant with industry standards. By leveraging Zenith’s innovative and reliable equipment, plant designers can ensure their operations are set up for success, with the flexibility to adapt to future industry developments and demands.