Don't miss our holiday offer - 30% OFF!
The Step-by-Step Manufacturing Process of Stone Crusher
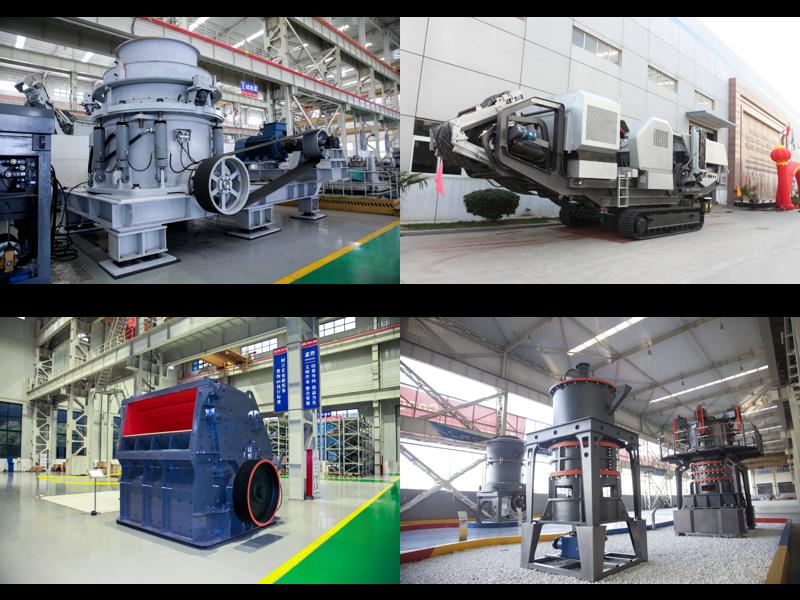
Introduction
The manufacturing process of stone crushers is a fascinating journey that unveils the intricate craftsmanship and engineering behind these powerful machines. Stone crushers play a crucial role in various industries, from construction to mining, as they are essential for breaking down large rocks and stones into smaller, more manageable pieces. Understanding the step-by-step process of how stone crushers are manufactured is not only educational but also provides insights into the quality, efficiency, and reliability of these machines.
In this article, we will take you on a comprehensive tour through the entire manufacturing process of stone crushers. From the initial extraction of raw materials to the final assembly and quality control, each stage is a critical part of ensuring that these machines perform their task effectively and safely. Whether you’re a professional in the industry or simply curious about how these impressive machines are made, this exploration into the world of stone crusher production promises to be an enlightening journey. So, let’s delve into the first stage: Raw Material Extraction.
1. Raw Material Extraction
The journey of a stone crusher begins with the first and fundamental stage: raw material extraction. The choice of raw materials is a crucial decision that impacts the performance and longevity of the finished stone crusher.
Selecting the Right Type of Stone
The process starts with identifying the appropriate type of stone to be used. Common options include granite, basalt, limestone, and others, each with its unique properties and suitability for specific applications. Factors such as hardness, durability, and composition are carefully considered to ensure the final product meets the required standards.
Quarrying and Mining Operations
Once the type of stone is determined, quarrying or mining operations commence to extract the chosen raw material. This stage involves the excavation of large blocks or fragments from the earth’s crust, usually from quarries or mines. It’s a physically demanding and often labor-intensive process that requires heavy machinery and skilled personnel.
Environmental Considerations in Raw Material Extraction
In recent years, environmental concerns have become increasingly important in raw material extraction. Sustainable quarrying and mining practices are being implemented to minimize the ecological footprint of these operations. This includes reclamation efforts, habitat restoration, and responsible land management.
Understanding the complexities of this initial stage is vital, as it sets the foundation for the entire stone crusher manufacturing process. The quality and suitability of the raw material will significantly influence the performance and durability of the final product. As we move forward, we’ll explore how these extracted materials are prepared for the next steps in the manufacturing journey.
2. Material Preparation
After the raw materials have been extracted, they undergo a series of essential preparation steps before they can be used in the manufacturing of stone crushers.
Crushing and Sizing of Raw Materials
The extracted raw materials, typically in the form of large rocks and stones, must be crushed and sized to meet the specific requirements of the stone crusher. This involves the use of specialized machinery such as crushers, screens, and conveyors. Crushing reduces the raw materials into smaller, more manageable pieces that can be further processed.
Quality Control Measures
Quality control is paramount during the material preparation stage. Rigorous testing and inspection are conducted to ensure that the crushed materials meet the desired specifications. Any variations or deviations from the standards are addressed promptly to maintain the consistency and quality of the raw materials.
Ensuring Consistency in Material Properties
Consistency in material properties, such as particle size, composition, and hardness, is crucial for the performance and reliability of the stone crusher. Manufacturers go to great lengths to maintain uniformity in their raw materials to guarantee the consistency of the final product.
Material preparation sets the stage for the subsequent phases in the manufacturing process. The precision and attention to detail during this stage are essential in ensuring that the stone crusher operates effectively and efficiently when put into action. In the next section, we’ll delve into the fascinating world of component fabrication, where the various parts of the stone crusher come to life.
3. Component Fabrication
Once the raw materials have been prepared, it’s time to delve into the intricate process of fabricating the various components that make up a stone crusher.
Design and Engineering of Crusher Components
Before fabrication begins, detailed design and engineering work are carried out. This involves creating blueprints and schematics for each component, taking into account factors such as load-bearing capacity, wear resistance, and efficiency. Modern CAD (Computer-Aided Design) software plays a vital role in this stage, allowing engineers to create precise plans for the components.
Material Selection for Crusher Parts
Choosing the right materials for each component is critical to ensure durability and longevity. Components like crusher jaws, cones, and impactors often use high-strength steel alloys that can withstand the immense pressures and abrasive forces encountered during crushing operations. The selection process involves balancing factors like hardness, toughness, and cost-effectiveness.
Precision Machining and Fabrication Techniques
The fabrication of components is a highly specialized process that involves cutting, shaping, and forming materials according to the design specifications. Precision machining techniques, such as CNC (Computer Numerical Control) machining, are commonly employed to achieve the exact dimensions and tolerances required for each part. Skilled machinists and fabricators work meticulously to bring the designs to life.
Component fabrication is a critical phase where the expertise of engineers and machinists comes into play. The quality and precision of these components directly impact the performance and reliability of the stone crusher. In the next section, we will explore how these meticulously crafted components are assembled and integrated to create the final product.
4. Assembly and Integration
With the components fabricated to precision, it’s time to bring together all the elements that make up a stone crusher through the assembly and integration stage.
Bringing Together All Crusher Components
In this phase, skilled technicians meticulously assemble the various parts that have been manufactured. This includes attaching crusher jaws, installing bearings, connecting belts and pulleys, and integrating electrical and hydraulic systems. The goal is to create a cohesive and functional unit that can effectively perform its crushing tasks.
Balancing and Aligning Mechanisms
Proper balancing and alignment are crucial to ensure the smooth and efficient operation of the stone crusher. Imbalances or misalignments can lead to premature wear and tear, reduced efficiency, and potential safety hazards. Technicians use specialized tools and equipment to achieve the precise balance and alignment required.
Quality Assurance in Assembly
Quality control is maintained throughout the assembly process. Rigorous checks and inspections are conducted to verify that each component is correctly installed and functioning as intended. Any deviations or issues are addressed promptly to ensure the final product meets the highest standards.
The assembly and integration stage is where the individual components come together to form a fully operational stone crusher. The craftsmanship and attention to detail during this phase are essential to guarantee the reliability and performance of the machine. In the next section, we will explore the critical step of testing and quality control to ensure that the stone crusher meets its intended specifications and standards.
5. Testing and Quality Control
Before a stone crusher can be considered ready for use in the field, it must undergo rigorous testing and quality control measures to ensure its performance, safety, and reliability.
Performance Testing of the Stone Crusher
Performance testing is a critical step in the manufacturing process. The stone crusher is subjected to various tests to assess its crushing capacity, efficiency, and overall functionality. These tests often involve running the machine with different types and sizes of raw materials to simulate real-world operating conditions.
Safety Checks and Quality Control Procedures
Ensuring the safety of the stone crusher is of paramount importance. Comprehensive safety checks are conducted to identify and rectify any potential hazards or malfunctions. This includes verifying that all safety features and emergency shutdown mechanisms are in proper working order.
Addressing and Rectifying Any Issues
During testing, any issues or deviations from the desired performance are carefully documented and addressed. This may involve fine-tuning the machine, making adjustments to components, or replacing parts that do not meet the required standards. The goal is to achieve optimal performance and reliability.
Once the stone crusher successfully passes all tests and quality control procedures, it is considered ready for deployment in various applications, such as construction, mining, and aggregate processing.
In conclusion, the testing and quality control phase is the final checkpoint in the manufacturing process, ensuring that the stone crusher meets the highest standards of performance, safety, and reliability. This marks the completion of our journey through the step-by-step manufacturing process of stone crushers.
Conclusion
The manufacturing process of stone crushers is a meticulous and complex journey that culminates in the creation of powerful machines vital to numerous industries. These crushers are the backbone of operations in construction, mining, and aggregate processing, as they transform large rocks and stones into smaller, manageable pieces. Understanding the manufacturing process not only sheds light on the craftsmanship and engineering behind these machines but also highlights the importance of quality and precision.
As we wrap up our exploration of the stone crusher manufacturing process, it’s essential to reflect on a few key points:
- Role in Various Industries: Stone crushers are indispensable tools in construction projects, where they help break down concrete and rocks, and in mining operations, where they crush ore and minerals. They are also crucial in the production of aggregates for roads and infrastructure projects.
- Ongoing Maintenance: To ensure the longevity and optimal performance of stone crushers, regular maintenance and servicing are imperative. This includes replacing worn-out parts, lubrication, and monitoring for any signs of wear or malfunction.
- Future Trends: The field of stone crusher manufacturing continues to evolve with advancements in materials, technology, and automation. Future trends may involve the use of more durable and sustainable materials, increased automation for efficiency, and enhanced safety features.
In closing, the manufacturing process of stone crushers is a testament to human ingenuity and engineering prowess. These machines have a profound impact on modern infrastructure and play a pivotal role in shaping the landscapes of our world. Whether you’re involved in the industry or simply curious about the behind-the-scenes process, understanding the journey from raw materials to functional machinery offers a newfound appreciation for these essential tools.