Don't miss our holiday offer - 30% OFF!
High-efficiency Sand Washing and Drying Equipment: Solution to Increase Production Capacity by 30%
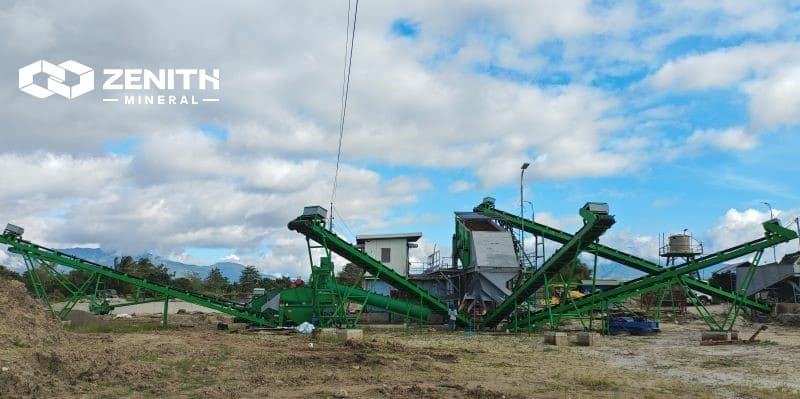
In the competitive world of construction and industrial mineral processing, achieving optimal production capacity is key. High-efficiency sand washing and drying equipment present a strategic advantage, promising up to 30% increased efficiency. Explore how these innovations can transform your operations and elevate your output in this comprehensive guide.
Understanding the Basics of Sand Washing and Drying
Sand washing and drying are critical processes in industrial sand production, ensuring that raw materials meet the required standards for construction, manufacturing, and other applications. These processes remove impurities, such as clay, silt, and organic matter, while reducing excess moisture, which is crucial for maintaining the structural integrity and usability of the final product.
Traditional Methods and Their Limitations
Conventional sand washing typically involves water-intensive techniques, such as wheel bucket systems or screw washers, which rely on high volumes of water to separate contaminants from the sand. While effective for basic cleaning, these methods often leave fine sand particles unrecovered, resulting in material loss and inconsistent quality. Furthermore, the drying process traditionally employs static or rotary dryers, which consume significant energy and fail to achieve uniform moisture reduction, leading to inefficiencies in downstream processing.
Role in Industrial Applications
High-quality sand is indispensable for industries like construction, glass manufacturing, and foundry casting. Any impurities or residual moisture can compromise the performance of the end product. Traditional equipment struggles to meet the increasing demands for precision and efficiency, prompting a need for advanced solutions.
Contribution
Zenith’s VSI6X Sand Crusher and HPT Cone Crusher integrate seamlessly into modern sand processing systems, offering enhanced sand shaping and impurity removal. Recent projects utilizing Zenith’s K3 Portable Crushing Plant have demonstrated improved throughput and cleaner outputs, paving the way for more efficient drying and reduced operational costs. These innovations set the stage for the high-efficiency systems discussed in subsequent chapters.
Innovations in Sand Washing Technology
The sands of change have swept over traditional processing methods, leading to significant innovations in sand washing equipment. These advancements are characterized by enhanced energy efficiency, meticulous water conservation, and sophisticated filtration systems that collectively amplify production capacities by around 30%.
State-of-the-art sand washing plants now employ energy-efficient motors and drives, reducing the power consumption of the entire process. This is evident in the HPT Cone Crusher and VSI6X Sand Crusher from Zenith, which integrate advanced hydraulic and automation technologies for optimized performance and reduced wear and tear.
Water conservation is a critical feature, as new systems recycle up to 95% of process water. This drastic improvement is pivotal in regions facing water scarcity. Filtration technology, too, is seeing a revolution, with multi-stage systems ensuring unparalleled purity of washed sand. Zenith’s innovative S Cone Crusher efficiently separates impurities, ensuring only high-quality sand reaches the next stage.
For instance, one case study involving Zenith’s equipment in a coastal facility showed a 35% increase in clean sand output, coupled with a 25% decrease in energy costs. These tangible benefits contribute to a lower carbon footprint and reduced operational expenses. Innovations such as these underscore the importance and impact of cutting-edge technology in transforming the sand processing landscape, setting the stage for more efficient drying techniques in subsequent stages.
Enhancements in Sand Drying Processes
Modern sand drying techniques have revolutionized the sand processing industry, significantly boosting efficiency and production capacity. Innovations such as fluidized bed dryers and rotary dryers play a pivotal role in complementing the washing process by drastically reducing drying time and energy consumption.
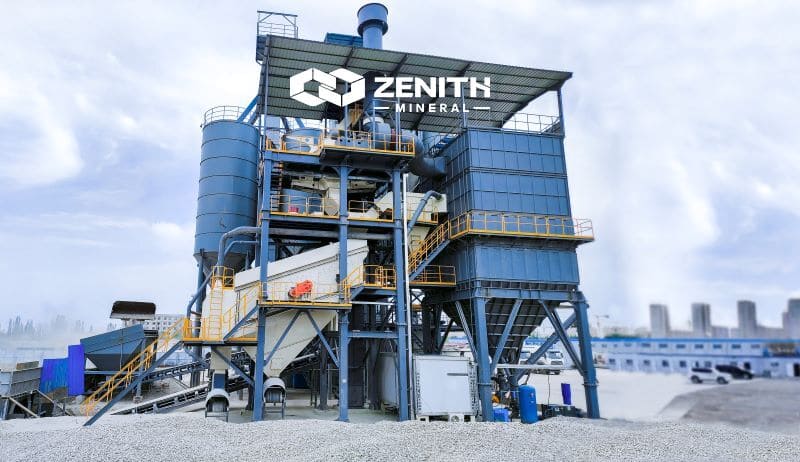
Fluidized bed dryers are particularly effective due to their ability to maintain uniform drying temperatures and their efficiency in handling a high throughput of sand. The process involves suspending sand particles in a stream of hot air, which ensures even drying and prevents overheating, thus preserving the quality of the sand. This technology considerably trims down energy use, making it a sustainable choice for large-scale operations.
On the other hand, rotary dryers offer robust performance with their rotating drum design, which ensures consistent exposure of sand particles to hot air. This design enhances heat transfer efficiency and minimizes drying time, making it ideal for operations requiring rapid processing.
These advancements work in synergy with equipment like the VSI6X Sand Crusher and PF Impact Crusher, known for their high efficiency and reliability in sand processing projects worldwide. For instance, in a recent project, integrating these advanced dryers with Zenith’s crushers led to a remarkable 30% increase in production capacity.
Such enhancements not only streamline the entire sand processing operation but also position operations to achieve higher throughput and reduced operational costs, setting a new benchmark in the industry.
Integrating Solutions for Maximum Efficiency
Integrating high-efficiency sand washing and drying equipment into existing operations involves strategic planning and practical considerations to ensure seamless adoption. Key to this process is assessing compatibility with current systems and minimizing operational disruptions.
Installation Ease and Compatibility: When integrating equipment like the VSI6X Sand Crusher or CI5X Impact Crusher, evaluate the spatial and infrastructural requirements. These systems are designed for straightforward installation, aligning with existing conveyor belts and power sources to reduce downtime.
Planning for Integration: Begin with a thorough audit of current systems to identify bottlenecks and potential areas of improvement. Collaborate with engineers to design an integration plan that includes phased implementation. This minimizes disruption while allowing for real-time adjustments. For instance, deploying the NK Portable Crushing Plant offers flexibility and ease of mobility, making it an ideal choice for sites undergoing gradual upgrades.
Return on Investment (ROI): High-efficiency systems promise significant ROI through increased production capacity and reduced energy costs. Using equipment such as the HPT Cone Crusher can lead to a 30% boost in processing efficiency, as demonstrated by Zenith’s project in Southeast Asia, where the integration of advanced crushers resulted in substantial operational improvements.
Ensuring Maximum Gain: Regular training sessions for operational staff on new equipment functionalities ensure optimal use and maintenance. Monitoring systems can be installed to provide data-driven insights, facilitating continuous improvement and maximizing the benefits of the new setup.
By carefully considering these aspects, businesses can effectively integrate cutting-edge technology, leading to enhanced productivity and profitability.
Conclusions
Adopting high-efficiency sand washing and drying equipment can significantly boost production, with potential increases up to 30%. By understanding the innovations available and strategically integrating them into existing workflows, businesses can achieve enhanced performance and reduced operational costs. Embrace these advancements to stay competitive and meet the growing demands of the industry.